Fuel Contamination Control
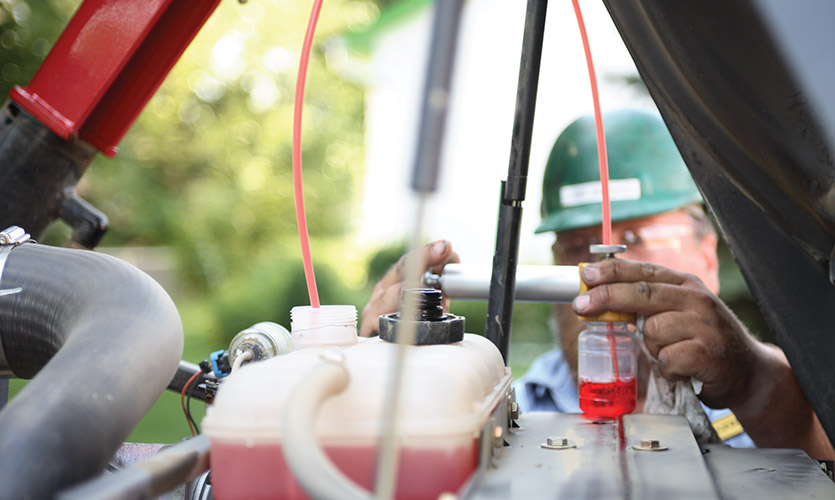
Clean Up Your Act
Fuel system contamination can cause serious problems in any diesel engine. But today’s high-performance, low-emissions models are especially vulnerable to contaminants. Keeping your fuel supply clean is vital to ensuring your engine can provide optimal performance and the longest service life possible.
While diesel is inherently up to 35% more efficient than gasoline, it comes with a few distinct challenges. It tends to attract water, which can be a serious concern if it enters a fuel system. Since water contains oxygen, it serves as sustenance for microorganisms, allowing them to grow and thrive in your fuel tanks. This condition is commonly known as diesel bug. It results in sludge that can clog your fuel injectors and cause engine failure.
Even before a clog forms, contaminated fuel lowers a diesel engine’s efficiency. When diesel costs nearly 54% more than it did just a few years ago, this loss of efficiency translates to a significant impact on a company’s bottom line. That makes fuel contamination control a critical concern for any fleet manager.
Eight Ways to Control Fuel System Contamination
When you’re managing a construction fleet, pausing operations to replace fuel system components can cost you a lot in the form of lost revenue and productivity — on top of the repair expenses.
Fuel filters play a role in cleaning diesel before it reaches the engine. Taking additional, proactive measures at the mechanical, sourcing and operational levels will also contribute to maintaining a clean supply of diesel by keeping contamination to a minimum. Take these steps to control fuel contamination:
- Know the numbers: Diesel fuel filters are commonly rated for a minimum particle size of anywhere from four to 15 microns. Even a 5-micron particle can cause engine damage, so for maximum protection, select a filter that’s effective against an absolute rating of 4-micron and larger particles.
- Don’t be misled by ambiguous filter rating systems: Focus on product features, structural integrity and consistency of quality. Do your research and choose a filter manufacturer with an established reputation. Components may cost a little more with this approach, but their contribution to your fuel contamination control efforts will pay off in terms of equipment efficiency and life expectancy.
- Find out about the wear index: A filter’s wear index is based on a correlation between the amount of physical damage observed on the injectors and the number of 6-, 10- and 14-micron particles present in the fuel. Determine if a lower-wear-index product is available to extend injector life, improve fuel economy and reduce emissions.
- Invest in premium quality filtration products: Look for filters with high-efficiency media, excellent pleat stability and spacing, a minimum number of metallic components, exceptional sealing capabilities and overall structural integrity.
- Buy fuel from a reliable supplier: Fuel quality and cleanliness vary from one supplier to the next, so make sure you’re buying from someone you trust. Because diesel is hygroscopic, it’s impossible to keep it entirely free of water. However, the water naturally settles to the lowest point in a tank, so it’s relatively easy to remove. A good supplier will monitor and purge their tanks as needed to ensure their fuel is as pure as possible upon delivery.
- Manage fuel storage and transfer: You’ll need to drain water that accumulates in the bottom of your storage tanks as well. Additionally, to keep sediment, dirt and other contaminants out of your fuel supply, you should drain and flush all storage containers, including tanker trucks and stationary tanks, every six months at a minimum. You should also frequently verify that your tanks are in good repair and have no worn, broken or missing parts. If you don’t already have a tank gauging system in place to monitor fuel purity, you might consider installing one.
- Involve operators: Operators play a key role in reducing fuel system contamination. At the start of each shift, they should perform a quick visual inspection of the fuel system components and the fuel itself — diesel that appears hazy is likely contaminated. During the hotter times of the year, when the heat supports microbe growth, you might consider having your operators drain the water from the bottom of your machines every day to keep your diesel as clean as possible.
- Train technicians: Contaminants often invade an engine while it’s being serviced. Technicians should be taught to use proper maintenance and repair processes to minimize service-related contamination. Similarly, operators should follow manufacturer recommendations and any additional operational standards when accessing tanks or handling fuel system components.
Another important element of maintaining a clean diesel supply and a healthy fleet is regular fuel testing. Warren CAT provides S·O·S? Fluid Analysis services to detect machine health indicators in fuel, hydraulics and other vital fluids. If you’re already following the above tips and want to evaluate the success of your fuel contamination control procedures, reach out to our team online or at 866-292-7736 to learn more.