How to Estimate Equipment Costs in Construction
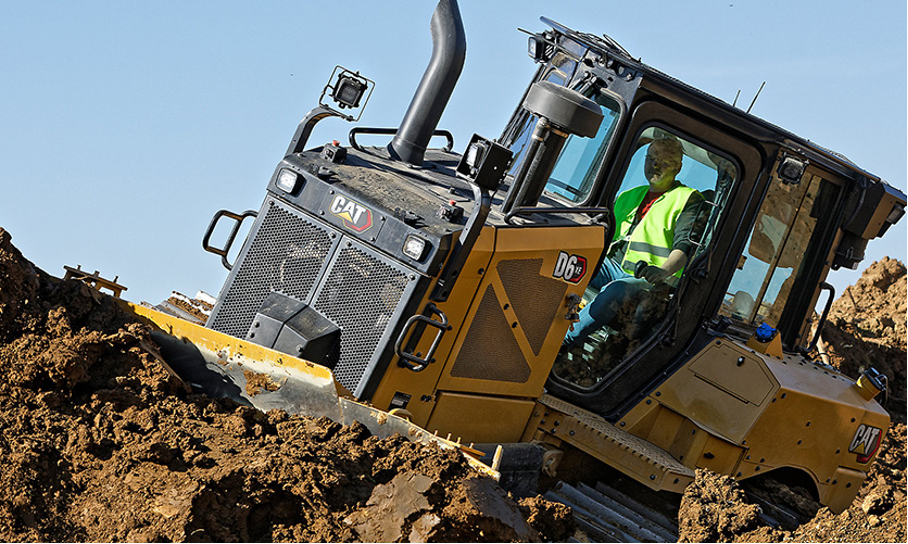
Cost management is a vital component for construction businesses and contractors. Equipment expenses make up a significant portion of monthly and annual costs, whether you purchase, finance or rent. By researching expected costs, you can make more informed decisions about your budget.
Equipment expenses vary depending on machine type, insurance requirements, maintenance needs, the type of work being performed and other related factors. Estimating construction equipment costs helps you maintain profitability and prepare for success. Learn more about how to estimate equipment costs in construction with this guide.
What to Consider When Calculating Equipment Costs
Many factors impact heavy equipment prices. When purchasing new equipment, you encounter both fixed and variable costs. Fixed prices are upfront and typically occur once, while variable prices change and can happen multiple times. Learning more about these factors helps you estimate the most accurate expected expenses.
1. Average Equipment Prices
The first fixed cost for equipment is its base price. Heavy equipment costs vary depending on several factors:
- Model: Manufacturers frequently introduce new models with new features and capabilities. For instance, new models can incorporate advanced technology that allows for more efficiency and accuracy. Older models might cost less than new ones, depending on their condition and features.
- Size: Construction equipment is available in many sizes, depending on the model’s load capacity, power, weight and other dimensions. Larger sizes often cost more than smaller sizes due to their additional capability.
- Condition: You can find heavy machinery in varying conditions, depending on their age and usage levels. Most equipment providers carry both new and used models and can give comprehensive details about the model’s history. Used options usually have lower prices than new models but might have more wear.
You should also factor in resale value. Many contractors or businesses purchase equipment and resell it later when it no longer meets their needs. Both new and used models can have high resale values if the equipment receives proper maintenance and care.
Different equipment types vary in price. You can either pay the full cost upfront or choose a financing option that spreads out your payments over months or years.Some construction teams prefer to rent equipment, which makes it easier to control overhead expenses and calculate equipment costs per hour or day.
Below are a few of the most popular heavy equipment types and their average costs:
- Excavators: Hydraulic excavators are popular and versatile tools, able to dig and move significant amounts of earth. They’re available in many sizes and specifications and therefore come in a wide range of prices. Compact sizes suit more precise and smaller applications and typically cost between $25,000 and $90,000. Standard-sized and larger-sized excavators can cost between $100,000 and $850,000.
- Dozers: Dozers are powerful pieces of equipment available in compact and large sizes. They are useful for various applications, from earthmoving to site preparation. Smaller models can cost about $40,000, while larger options can sell for over $500,000.
- Skid steers: Skid steers and compact track loaders are versatile options for digging, lifting and other applications. They have various sizes, attachments and features, making their costs vary. A new, standard-sized skid steer can range from $17,000 to well over $50,000.
2. Insurance Costs
Insurance is an essential variable cost for equipment purchases. Insurance provides coverage for damages, theft, breakdowns and other instances that impede a construction site’s efficiency. Depending on your insurance plan, the provider might cover part or all of the related fees. Other insurance options provide reimbursements for business interruptions that occur during machine downtime.
Insurance costs vary depending on the provider, equipment cost, construction site specifications and other factors. Insurance providers can offer specific quotes for monthly or annual rates. Safety also plays an important role, as your rate might increase if you experience frequent accidents.
3. Repair Costs
Another variable expense is the cost to repair your equipment. Regularly used equipment is susceptible to wear and can sustain damage over time. It’s important to repair equipment quickly to maintain its condition and keep your construction site working safely and at peak efficiency.
It can be challenging to estimate annual repair costs because they vary in severity and frequency. The more you use equipment, the more wear it endures. The environmental conditions you typically work in directly impact machine wear and tear, and especially harsh job site conditions can result in increased repair needs.
Repairs can consist of a single part breaking or an entire machine breakdown, leading to a wide difference in potential costs. Machines in poor condition might also need repairs more frequently than new machines.
Common heavy equipment repairs include:
- Engine: Basic repairs, like replacing a sensor or gaskets, can cost a few hundred dollars or upwards of a couple thousand dollars. Rebuilding or overhauling an engine can cost anywhere from a few grand to more than $20,000.
- Hydraulic system: Minor repairs, such as swapping out a seal or hose, can range between a couple hundred to a couple thousand dollars. More serious hydraulic repairs can cost upwards of $10,000.
- Structural: The average costs of structural damage will vary depending on severity and location. Extensive repairs can potentially cost tens of thousands of dollars.
4. Preventative Maintenance Costs
Regular maintenance is vital for heavy equipment and helps you identify potential problems before they grow into more significant and costly issues. Tasks like oil changes, wire replacements and track adjustments are essential for efficient operation and machine life span.
Even though proper maintenance can provide significant cost savings, these tasks still add to your equipment costs. Many businesses and contractors partner with providers for specialized maintenance plans, which can have monthly or annual fees. However, these costs even out — maintenance helps you increase equipment life spans and boost overall productivity, resulting in long-term gains.
5. Fuel Costs
Fuel costs are another significant consideration for equipment owners, contributing between 30% to 50% of overall expenses. Your equipment’s fuel use depends on many factors, making your overall cost vary each month. For instance, fuel costs are based on:
- Fuel efficiency: The rate your equipment consumes fuel varies by machine and work type. Certain models might consume fuel faster than others, causing you to spend more. Many other features impact fuel efficiency, including operating techniques, equipment application or onboard technology.
- Diesel fuel value: Fuel prices change constantly, which can make your monthly costs unpredictable. Most heavy equipment runs on diesel fuel, and its price differs depending on market availability, labor costs, taxes and other factors.
Each machine type consumes fuel at a different rate, and the cost of fuel can change quickly, making it harder to estimate costs.
6. Work Type and Conditions
The type of work you typically complete will also impact equipment costs. Consider the strain your common applications and job site conditions can have on your fleet. For example, a wheel loader used primarily for moving sod on landscaping projects will likely have lower operating costs and fewer repair needs than a loader used for hauling boulders in rock quarries.
Your unique project requirements directly influence how hard your equipment must work and how efficiently it can complete tasks, which will ultimately affect your ownership costs.
Contact Warren CAT for Deals on Construction Equipment
The more you understand typical heavy equipment expenses, the better you can prepare your budget for upcoming projects. In addition to upfront costs, you need to manage ongoing insurance, maintenance and fuel fees.
Warren CAT offers a wide range of new, used and rental heavy equipment to meet project requirements of any size. We help you find the best fit from our broad inventory of reliable and heavy-duty equipment. We also offer many financing options that make payment processes flexible and transparent.
Contact Warren CAT today to learn more about our available construction equipment.