How Technology Is Making Construction Safer
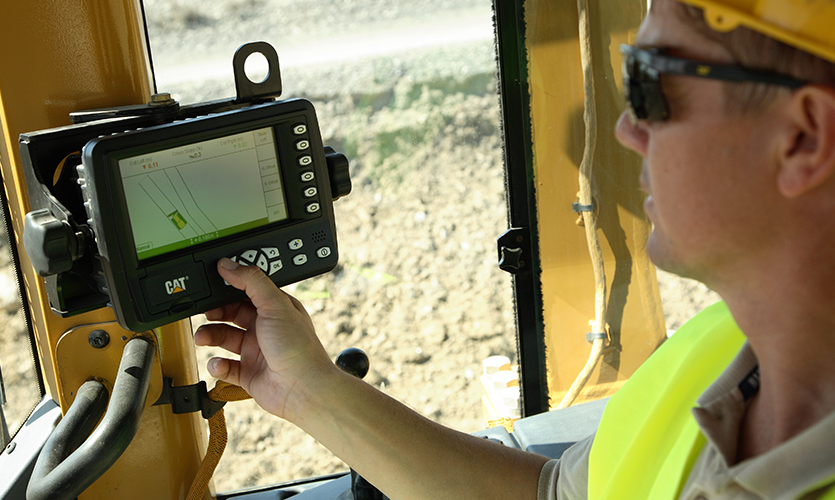
Technology continues to change construction sites by improving both efficiency and safety. Through innovations in remote communications, employers have even more significant influence over the safety of their work crews and jobsites. Discover the construction equipment that integrates the latest in safety advances.
Jump To Sections:
- The Importance of Safe Construction Sites
- Construction Safety Technology
- Cat Technology for Improved Safety
- Warren CAT Construction Technology
Importance of Safe Construction Sites
Construction ranks as one of the most dangerous sectors for workers. Of workplace fatalities in 2017, one fifth came from the construction industry. Most of the deaths, 59.9 percent, happened from one of four causes:
- Falls: Falls caused the deaths of 386 construction workers in 2017, placing this reason as the most common cause of death among workers on construction sites.
- Struck by Objects: Construction workers hit by objects, either falling from a height or flying through the air, accounted for 8.2 percent of fatalities.
- Electrocution: Close behind those injured by objects is the number of those electrocuted. This injury was the cause of 7.3 percent of deaths in construction workers.
- Caught by Objects: Construction crew members caught between objects or compressed by objects was the fourth leading cause of death with 5.1 percent.
The Occupational Safety and Health Administration, OSHA, enforces regulations to prevent injuries and deaths on jobsites across multiple industries. From October 2017 through September 2018, the top violations for all sectors included many specific to construction:
- Fall Protection: Employers must protect workers from falls. Failing to adhere to OSHA guidelines puts employees at risk from the leading cause of construction worker deaths.
- Scaffolding: Setting up safe, stable scaffolding prevents both people and objects from falling. Due to the increased chances of injury, OSHA creates strict requirements for using scaffolding on a jobsite.
- Ladders: Failing to safely use ladders can earn a jobsite an OSHA violation.
- Other Violations: General industry violations overlap with many construction site hazards. Other violations on the top 10 list from OSHA for 2018 included powered industrial trucks, failing to train for fall protection, guarding machinery, controlling hazardous energy sources and failing to wear adequate eye or respiratory protection.
Clearly, maintaining safety on construction sites should be paramount. Older technologies cannot solve problems such as fatigued operators, workers in dangerous positions on the ground and equipment problems. Thanks to innovations in the field, though, tracking the safety and productivity of construction workers has never been easier.
Technology in Construction
While you may think of the heavy, mechanical equipment used in construction as relics of a bygone era, the technology under the hood and around the jobsite belie that idea. Some ideas have become mainstream and used in many types of equipment. Other innovations remain in the planning stages, still awaiting further testing to prove their merit in the field.
Companies introduce new ideas to solve existing problems on the jobsite, and safety ranks high among those. Many inventions used on today’s construction machinery makes the devices safer to use while protecting the operator and those nearby.
Though adopting the latest ideas requires a significant investment, you can see a return. Investing in construction safety technology can save you money from injuries, lost productivity and downtime due to accidents.
Construction Safety Technology
Many companies embrace the notion of integrating technology into their construction sites for increasing worker safety. Methods vary from drones to wearable technology and tracked equipment. Before you choose to purchase every safety feature sold for your jobsite, though, take a look at your latest safety evaluation. Get items to help your site improve in areas that most need an increase in safety. Doing so will ensure you make a wise investment in technology, especially when you consider how many options you have.
1. Drones
Camera-equipped drones allow you to quickly oversee the jobsite without putting yourself or other workers at risk. With a small eye-in-the-sky drone, you can watch to ensure your workers follow safety protocols. Unlike some other technologies, drones are consumer products you can purchase from an electronics store. With multiple options, look for the most durable model possible.
Some worksites even use drones to carry small pieces of equipment or tools. When sending a drone for this application, choose a heavy-duty drone with extra lift. This application becomes especially useful on multi-story jobsites or those that cover large amounts of land. A drone can pass over the travel distance in much less time than a person.
The cameras on drones also allow workers to glimpse into spaces that may be too dangerous for humans to enter such as entering buildings for demolition or inspecting bridges. Using machines instead of humans helps keep human employees safe without compromising productivity.
2. Smart Clothing
Personal protective equipment, PPE, places a barrier between the body and hazards of a particular worksite. As technology becomes more integrated into the workplace, it also includes the clothes worn for protection on the jobsite. Smart clothing can be as simple as hard hats with built-in carbon monoxide, CO, detectors. Being able to alert a worker of the presence of colorless, odorless CO could save a life.
Other types of smart clothing have greater connectivity to a more extensive information grid. A geofence, an electronically created virtual barrier, alerts supervisors or sounds an alarm if workers pass through into a prohibited area. Other types of garments measure worker physical signs such as breathing, heart rate and skin temperature. An elevation in these could indicate heat illness that requires immediate treatment. Some sensors will even detect a shift in worker posture, possibly indicating fatigue.
3. Virtual Reality and Augmented Reality
Instead of turning new operators over to heavy equipment, consider integrating virtual reality or augmented reality into the training program. Virtual reality requires the user to interact with an entirely computer-generated world to learn the basics of machine operation and safety protocols.
Augmented reality takes the training to the next level by putting a computerized overlay over a pair of clear glasses that also let you see and interact with the world around you. In an augmented reality training program, an operator can sit at the controls of a machine and interact with the controls in response to a variety of virtual challenges that reflect real-life situations. This type of training ensures all operators, even if licensed, are fully ready to use the heavy equipment specific to your jobsite without putting others in danger.
Augmented reality has a place in detecting dangers in the environment. Workers wearing a special helmet can see things like alert signs when they near potentially hazardous conditions. The system also allows employers to determine what information the workers see to help improve their safety and job functions.
4. Mobile Reporting
Equipping workers with mobile devices gives supervisors a way to track the location of each employee through GPS. The employees can also use the mobile devices to record incidences of safety violations or problems they see on the jobsite. GPS recording lets the supervisor know precisely where the problem occurred, making it easier to find and correct the issue in the future.
Mobile reporting can happen as soon as a problem occurs, not after working hours. Additionally, since everyone on site has a mobile device, reporting feels more anonymous than walking to a supervisor’s office. Workers may feel more comfortable reporting incidents over a mobile device. By not allowing problems on the jobsite to be ignored, mobile device incident reporting could be a way to make a smoother transition into safety technology integration into a jobsite.
The downside to mobile reporting is the connectivity required. Unless your jobsite has Wi-Fi or cellular connectivity, you cannot adopt mobile reporting for real-time monitoring of employee locations and incident reports. Some jobsites are so remote that even cell signals are impossible to get. For such instances, site monitoring of local sensors may be a better technological innovation.
5. Site Monitoring
The environmental conditions on a jobsite can contribute to worker health and safety, as well. Keeping tabs on temperature, dust, noise and chemical levels from sensors installed around the site allows supervisors to recommend workers clear the area if the levels get dangerously high. Workers may also get an alert if the chemical exposure levels get too high for safe operation in the area.
Regularly monitoring the jobsite for dangerous conditions also makes it easier for supervisors to mitigate the problem and make the entire area safer for workers by reducing the chemicals from the source or through enforcing heavier duty PPE.
Cat® Technology for Improved Safety
Caterpillar® knows how important workers’ safety is to a construction site. Injuries delay projects and take valuable expertise away from the project. To help you protect your workers, Caterpillar creates specific technology for its vehicles to ensure the safety of the operators and everyone on the site. Technology ranges from devices installed on the machine to those worn by workers.
1. Cat Connect
The Cat Connect line of technology includes multiple ways to make Cat heavy equipment more productive and safer. Components in the system include both hardware and software. Through combining these technologies with the machinery you already have, you can protect your workers from adding to the injury or fatality statistics on construction sites while minimizing downtime.
2. Built-In Operator Monitoring
Driver distractions and fatigue plague constructions sites just as much as they do the freeways. While cars don’t have means of preventing disturbances, Cat vehicles have built-in operator monitoring systems to deter dangerous driving.
In the cab, sensors track head and eye movement during operation to look for variances that could indicate distraction. The system even works if the driver wears sunglasses or operates the vehicle at night. When the system detects the driver may not pay enough attention to operating the vehicle, an alarm sounds and the seat vibrates, alerting the driver and hopefully restoring attention. Caterpillar Safety Advisors confirm and log the incident for reporting to the supervisor.
Fatigue is another serious concern for operators. As with distractions, in-cab sensors monitor the driver. In cases when the driver’s head nods or eyes close for too long, the seat vibrates and an alarm sounds. A tired driver requires more immediate care than a distracted one. Even after the in-cab alarm sounds, the Caterpillar Safety Advisor connected to the monitoring system sends an alert to the site supervisor, who can pull the operator from the vehicle and give them a chance to wake up.
The benefit of the Cat driver safety system is its flexibility. You can have the monitoring equipment installed in any heavy equipment you operate on your jobsite, new or used. While you can only get some safety features in new vehicles from the factory, the driver safety system fits onto the fleet you already have, making it a top choice if you have existing machinery you want to make safer.
3. Remote-Controlled Equipment
As some companies use drones to fly into dangerous areas, Caterpillar applies the idea to a larger scale. When you need to use your heavy equipment in hazardous conditions, instead of putting an operator at risk, use the Cat remote control choice of Cat Connect. This technology is just the first foray into autonomous construction vehicles without the safety concerns of allowing heavy equipment self-operation.
Remote operation from Caterpillar has two options. The company requires integration of either into a new machine. However, if you want an added safety feature on your new Cat equipment, consider ordering it with Cat Command remote operation hardware installed:
- Line-of-sight: For line-of-sight operation, the operator controls the vehicle while on site with it. This system does not require a consistent high-speed data connection on your jobsite. Using a portable controller, the operator stands within sight of the vehicle to move it. Choose this option for short-term solutions or if you need an emergency remote operation of your vehicles.
- Remote location: If you have a high-speed data connection with a centralized control station, you can allow operators to control vehicles in the comfort of an air-conditioned command center. Unlike line-of-sight use, having a remote location allows the operator to control vehicles all day if needed. You cannot overestimate the importance of a stable, high-speed wireless data connection for such a system. When seconds count, the system must instantly communicate the operator’s controls to the vehicle without interruption.
4. Worker Detection Systems
The Cat Detect uses several ways to alert operators of the location of other workers on the jobsite. Thanks to passive radio frequency identification, RFID, technology, the detection system will never return a false positive, ensuring the driver always knows where others are during vehicle operation. By alerting the operator of people around the vehicle, the number of accidents is reduced.
The Cat Detect system starts with small RFID sensors fitted into each worker’s reflective vest and hard hat. Workers never need to remove these washable sensors that don’t require a power supply. Unlike active RFID, the passive devices used in clothing for the Cat Detect system do not emit radio waves.
The detector on the vehicle searches for any sensors by sending out radio waves. Even workers sitting or lying on the ground will still have working sensors the Cat Detect system can find. When the detector sees a sensor, it alerts the driver visually and audibly on the in-cab display.
5. Wearables for Fatigue Detection
With monitoring, you will never have to worry if a worker is trying to “act tough” and fight against the fatigue. Even the most energetic people can succumb to their bodily functions, such as sleepiness, at some point. Not all construction workers will operate heavy machinery, but they still need to remain alert on the jobsite. A tired worker may become more dangerous and inaccurate even with simple tasks. To prevent dangerous situations, injuries and fatalities, Caterpillar developed a wearable technology to monitor the fatigue level for all workers on the site with the Cat Smartband.
The Cat Smartband collects information about the user’s sleep patterns, circadian rhythms and more to predict fatigue. Combining the software the band connects to and special software that uses bio-mathematical science to help the worker know even before work if he will feel sleepy on the job.
When each worker arrives on the site, they have a fatigue score, related to recent sleep patterns uploaded to the cloud from their Smartband as soon as they come on the jobsite. This score combines with other users’ ratings to create a report. The collective report on all workers helps supervisors decide who is awake enough to work safely and for how long. The report even includes how many hours a worker will be awake enough to work reliably and when they should move off the jobsite.
When the score drops below 70, the fatigue a worker feels creates behaviors and reaction times comparable to drunk driving. You wouldn’t want drunk employees on your jobsite. A tired worker can be just as dangerous. The technology of the Smartband and its accompanying analytical software make it easier than ever to prevent fatigue-related workplace accidents.
Reducing the number of fatigued workers on your site will also help productivity. Tired workers are more likely to make mistakes, leading to lowered productivity and a higher number of errors. By pulling fatigued workers off the jobsite and correcting their level of awareness, you can reduce downtime and continue to move forward on your project.
Learn More About Safe Construction Equipment
To find out how you can incorporate safer equipment, add-ons and vehicles to your fleet, check out our lineup at Warren CAT. Explore the ways Caterpillar has innovated construction equipment to maximize safety and reduce risk. Like Cat equipment, you can only get the latest in technology from the company through an authorized Cat dealer, like Warren CAT.
Safety devices from Caterpillar help make your jobsite safer in several situations, but you may not need all these innovations for your work conditions. If you need help deciding which of these products you need to improve your jobsite safety, talk to your nearest Warren CAT dealer. We can help you find the best Cat equipment and safety add-ons to optimize site safety and productivity.
As an authorized Caterpillar dealer, we have access to the durable and dependable equipment you have come to know from the brand. Our service area includes Oklahoma, West Texas and the Texas Panhandle. If you work in those areas, give us a call at 866-292-7736 for more information about improving your construction safety with Cat technology, equipment and vehicles. With new, used and rental heavy equipment in addition to parts and service at Warren CAT, you will get the heavy equipment and accessories your jobsite needs to finish the work.